Our product range
From strip for terminals and connectors through to stamped parts, our wide range of differing materials and surface finishes is appreciated all over the world and used by the main connector manufacturers in Europe, America and Asia. We guarantee always to provide you with user-oriented solutions tailored to your specific requirements. Building on our main cornerstones of function, appearance and reliability, we have proven ourselves and achieved absolute customer satisfaction year after year via exceptional conductivity, excellent corrosion resistance and good workability.
Chief advantages of KMD high-performance alloys:
- High electrical conductivity
- Good relaxation resistance – even at operating temperatures reaching 200°C
- High mechanical strength combined with good formability
- Good tooling life
- Good recyclability of stamping scraps, a valuable contribution to protecting the environment and reducing waste
- Materials with tensile strength up to 900 MPa
Download
Our technical handout can be found here.
Plain Strip
Use our plain strip as the basis for electrical and electronic applications in the automotive industry, as well as for communications and power supply.
STOL® high-performance alloys offer an unparalleled combination of electrical conductivity with strength and formability. The corson alloys STOL® 76, STOL® 76M and STOL® 94 also have particularly high resistance to stress relaxation.
Strip dimensions
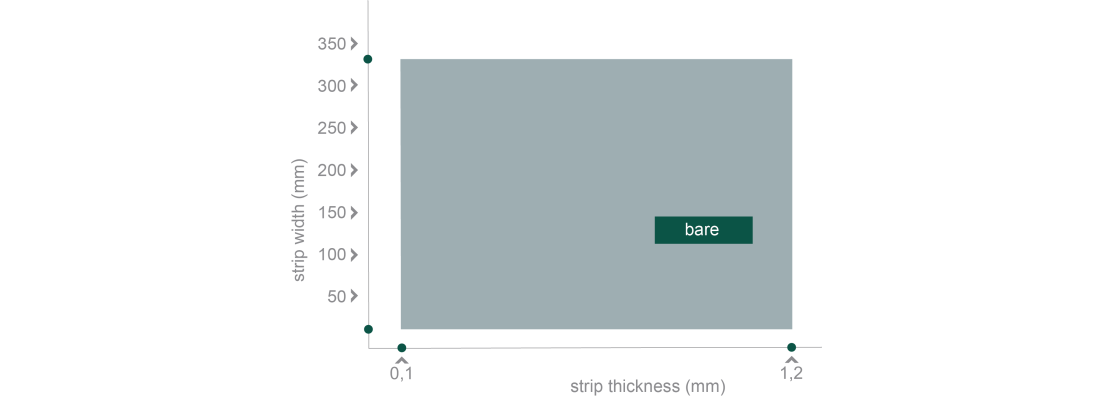
Tolerances
Strip Thickness
We offer strip in two differing classes of thickness tolerance, up to a maximum width of 330 mm.
Strip Thickness (mm) | Standard | Precision |
---|---|---|
0.08 – 0.20 | ± 0.005 | ± 0.004 |
0.21 – 0.30 | ± 0.007 | ± 0.005 |
0.31 – 0.40 | ± 0.015 | ± 0.006 |
0.41 – 0.50 | ± 0.015 | ± 0.008 |
0.51 – 0.60 | ± 0.017 | ± 0.010 |
0.61 – 0.70 | ± 0.020 | ± 0.010 |
0.71 – 0.85 | ± 0.022 | ± 0.012 |
0.86 – 1.20 | ± 0.025 | ± 0.015 |
Strip Width
We offer standard and precision tolerances on strip width too.
Strip Thickness (mm) | 10 – 50 | 51 – 100 | 101 – 200 | 201 – 330 |
---|---|---|---|---|
Standard | ||||
0.08 – 1.00 | + 0.20 | + 0.30 | + 0.40 | + 0.60 |
1.01 – 1.20 | + 0.30 | + 0.40 | + 0.50 | + 1.00 |
Precision | ||||
0.08 – 1.00 | + 0.10 | + 0.20 | + 0.30 | + 0.40 |
1.01 – 1.20 | + 0.20 | + 0.20 | + 0.40 | + 0.60 |
Alloys
For many years, we have produced differing high-performance semi-finished products for our customers in highly diverse industries, such as automotive, communications and electronics. Following our guiding principles, top quality has always remained our highest priority. This has helped us grow into a major global supplier of high-quality precision strip.
STOL® High Performance Alloys
Medium to high electrical conductivity, high strength, good formability and good to excellent resistance to stress relaxation.
Copper
Best electrical conductivity coupled with medium to low strength.
Brass
Most economical material for connectors, low electrical conductivity, medium strength and good workability.
Phosphor Bronze
Medium electrical conductivity, with good spring properties, but more expensive metal than copper and brass.
Segment A
Basic applications
= Low conductivity, medium to exceptional strengthSegment B
Electronics applications
= Medium conductivity, Medium to high strengthSegment C
Automotive applications
= Medium conductivity, Medium strengthSegment D
Electric vehicles and high-voltage applications
= Low to medium strength, high conductivity
Brass
DIN-EN | CEN | ASTM | JIS | BS | Conductivity ** | |||
---|---|---|---|---|---|---|---|---|
CuZn5 | CuZn5 | CW500L | C21000 | C 2100 | CZ125 | MS/m ≥ 33 | IACS(%) ≥ 56 | Details & Downloads CuZn5
Material designations
Conductivity ** Downloads |
CuZn10 | CuZn10 | CW501L | C22000 | C2200 | CZ101 | MS/m ≥ 25 | IACS(%) ≥ 43 | Details & Downloads CuZn10
Material designations
Conductivity ** Downloads |
CuZn15 | CuZn15 | CW 502 L | C23000 | C2300 | CZ102 | MS/m ≥ 20 | IACS(%) ≥ 34 | Details & Downloads CuZn15
Material designations
Conductivity ** Downloads |
CuZn30 | CuZn30 | CW505L | C26000 | C2600 | CZ106 | MS/m ≥ 16 | IACS(%) ≥ 28 | Details & Downloads CuZn30
Material designations
Conductivity ** Downloads |
CuZn33 | CuZn33 | CW506L | C26800 | C2680 | - | MS/m ≥ 15 | IACS(%) ≥ 26 | Details & Downloads CuZn33
Material designations
Conductivity ** Downloads |
CuZn36 | CuZn36 | CW507L | C27000 | C2700 | CZ108 | MS/m ≥ 14 | IACS(%) ≥ 24 | Details & Downloads CuZn36
Material designations
Conductivity ** Downloads |
CuZn37 | CuZn37 | CW508L | C27200 | C2720 | CZ107 | MS/m ≥ 14 | IACS(%) ≥ 24 | Details & Downloads CuZn37
Material designations
Conductivity ** Downloads |
Bronze
DIN-EN | CEN | ASTM | JIS | BS | Conductivity ** | |||
---|---|---|---|---|---|---|---|---|
CuSn4 | CuSn4 | CW450K | C51100 | C5111 | PB101 | MS/m ≥ 12 | IACS(%) ≥ 21 | Details & Downloads CuSn4
Material designations
Conductivity ** Downloads |
CuSn5 | CuSn5 | CW451K | C51000 | C5102 | PB102 | MS/m ≥ 10 | IACS(%) ≥ 17 | Details & Downloads CuSn5
Material designations
Conductivity ** Downloads |
CuSn6 | CuSn6 | CW452K | C51900 | C5191 | PB103 | MS/m ≥ 8 | IACS(%) ≥ 13 | Details & Downloads CuSn6
Material designations
Conductivity ** Downloads |
CuSn8 | CuSn8 | CW453K | C52100 | C5210 | PB104 | MS/m ≥ 6 | IACS(%) ≥ 11 | Details & Downloads CuSn8
Material designations
Conductivity ** Downloads |
Copper
DIN-EN | CEN | ASTM | JIS | BS | Conductivity ** | |||
---|---|---|---|---|---|---|---|---|
Cu-ETP | Cu-ETP | CW004A | C11000 | C1100 | C101 | MS/m ≥ 58 | IACS(%) ≥ 100 | Details & Downloads Cu-ETP
Material designations
Conductivity ** Downloads |
Cu-HCP | Cu-HCP (SE-Cu) | CW021A | C10300 | - | - | MS/m ≥ 57 | IACS(%) ≥ 98 | Details & Downloads Cu-HCP
Material designations
Conductivity ** Downloads |
Cu-PHC | Cu-PHC (SE-Cu) | CW020A | C10300 | C10300 | - | MS/m ≥ 58 | IACS(%) ≥ 100 | Details & Downloads Cu-PHC
Material designations
Conductivity ** Downloads |
Cu-DLP | Cu-DLP | CW023A | C12000 | - | - | MS/m ≥ 55 | IACS(%) ≥ 95 | Details & Downloads Cu-DLP
Material designations
Conductivity ** Downloads |
Cu-DHP | Cu-DHP | CW024A | C12200 | C1220 | - | MS/m ≥ 47 | IACS(%) ≥ 81 | Details & Downloads Cu-DHP
Material designations
Conductivity ** Downloads |
Cu-OFE | Cu-OFE | CW009A | C10100 | C1010 | - | MS/m ≥ 58 | IACS(%) ≥ 101 | Details & Downloads Cu-OFE
Material designations
Conductivity ** Downloads |
High Performance Alloys (HPA)*
DIN-EN | CEN | ASTM | JIS | BS | Conductivity ** | |||
---|---|---|---|---|---|---|---|---|
STOL®75 | - | - | C18070 | - | - | MS/m ≥ 45 | IACS(%) ≥ 78 | Details & Downloads STOL®75
Material designations
Conductivity ** Downloads |
STOL®76 | - | - | C19010 | - | - | MS/m ≥ 35 | IACS(%) ≥ 60 | Details & Downloads STOL®76
Material designations
Conductivity ** Downloads |
STOL®76M | - | CW109C | C19005 | - | - | MS/m ≥ 33 | IACS(%) ≥ 57 | Details & Downloads STOL®76M
Material designations
Conductivity ** Downloads |
STOL®78 | - | - | C18665 | - | - | MS/m ≥ 36 | IACS(%) ≥ 62 | Details & Downloads STOL®78
Material designations
Conductivity ** Downloads |
STOL®80 | - | CW177C | C14410 | - | - | MS/m ≥ 44 | IACS(%) ≥ 76 | Details & Downloads STOL®80
Material designations
Conductivity ** Downloads |
STOL®94 | - | - | C70310 | - | - | MS/m ≥ 25 | IACS(%) ≥ 43 | Details & Downloads STOL®94
Material designations
Conductivity ** Downloads |
STOL®95 | - | CW106C | C18160 | - | - | MS/m ≥ 50 | IACS(%) ≥ 86 | Details & Downloads STOL®95
Material designations
Conductivity ** Downloads |
C15500 | - | CW106C | - | - | - | MS/m ≥ 50 | IACS(%) ≥ 86 | Details & Downloads C15500
Material designations
Conductivity ** Downloads |
STOL®194 | - | CW107C | C19400 | - | - | MS/m ≥ 35 | IACS(%) ≥ 60 | Details & Downloads STOL®194
Material designations
Conductivity ** Downloads |
Special alloys
DIN-EN | CEN | ASTM | JIS | BS | Conductivity ** | |||
---|---|---|---|---|---|---|---|---|
CuNi3Si | CuNi3Si | C70250 | - | - | MS/m ≥ 23 | IACS(%) ≥ 40 | Details & Downloads CuNi3Si
Material designations
Conductivity ** Downloads | |
CuSn3Zn9/CuSn2Zn10 | CuSn3Zn9/CuSn2Zn10 | CW454K | C42500 | - | - | MS/m ≥ 15 | IACS(%) ≥ 25 | Details & Downloads CuSn3Zn9/CuSn2Zn10
Material designations
Conductivity ** Downloads |
Tinned strip
Ever-more exacting reliability requirements mean that electro-mechanical components are increasingly made from pre-tinned strip. Especially in the automotive industry, hot-dip tinning has proven itself time and time again to be the preferred option for corrosion protection and contact surfaces. Special tinning processes have been developed to permit higher operating temperatures, reduce mating / unmating forces, and minimise fretting corrosion.
Tin-Silver coating
Tin-silver coatings typically offer greater temperature stability and hardness than pure tin coatings. Tin-silver coatings on STOL® 76M or STOL® 94 alloys are suitable for applications hotter than 130°C. This is an entirely lead-free solution that significantly reduces whisker formation and allows soldering for up to six months.
KMD Coatings Beyond Tin-Silver
The table below gives an overview of the differing STOL® coating solutions for hot-dip tinned strip and the particular properties of each special tin coating.
Hot-Dip Tinning / Coating Types
STOL® Sn10 – Pure Tin
Standard coating with IMP*
Coating thickness determines advantages
STOL® Sn11 – Thin layer
Reduced mating and unmating forces, less prone to fretting corrosion,
IMP*: Sn = 1 : 1
STOL® Sn13 – Thermal Tin
Lowest mating and unmating forces, wear resistant
STOL® Sn14
More mating cycles possible, due to thicker IMP and pure-tin top layer
IMP*: Sn = 1 : 1
STOL® Sn28M – Tin-Silver
Operating temperatures up to 150°C possible, depending on coating combination
Hot-Dip Tinning
We can supply rolled strips with hot-dip tinned coatings that meet DIN EN 13148.
KMD's hot-dip tinned coatings are compliant with the EU RoHS Directive (Restriction of the Use of Certain Hazardous Substances in Electrical and Electronic Equipment. This directive restricts the use (and placing on the market) of hazardous substances in electrical devices and electronic components). The intrinsic process characteristics of hot-dip tinning enable coating with alloys. Hot-dip tinned strip is available up to 330 mm maximum width and between 0.15 and 1.5 mm thickness.
We are able to provide two in-house hot-dip tinning options: Mechanical Wipe Tinning (MWT) and Hot Air Levelled Tinning (HALT).
Hot-Dip Tinning to DIN EN 13148 (RoHs compliant)
Thickness: | 0.20 - 1.50 mm |
Width: | up to 330 mm |
Coatings: | pure tin, silver-tin, thermal tin |
Coating thickness**: | 1.0 - 3.0 μm 2.0 - 5.0 μm 4.0 - 10.0 μm 10.0 - 20.0 μm |
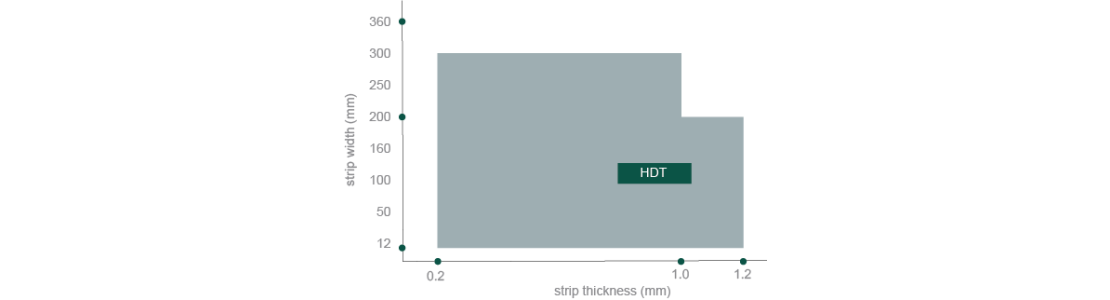
Electroplating
We manufacture electro-plated products according to DIN EN 14436. Via our external electroplating subcontractors, we are able to work with thicknesses from 0.40 to 2.00 mm in widths of up to 170 mm.
Electroplating to DIN EN 14436 (RoHS compliant)
Thickness: | 0.2 - 4.00 mm |
Width: | up to 300 mm |
Coatings: | Sn on Cu and Sn on Ni |
Coating type: | fully plated, dull, bright, or reflow |
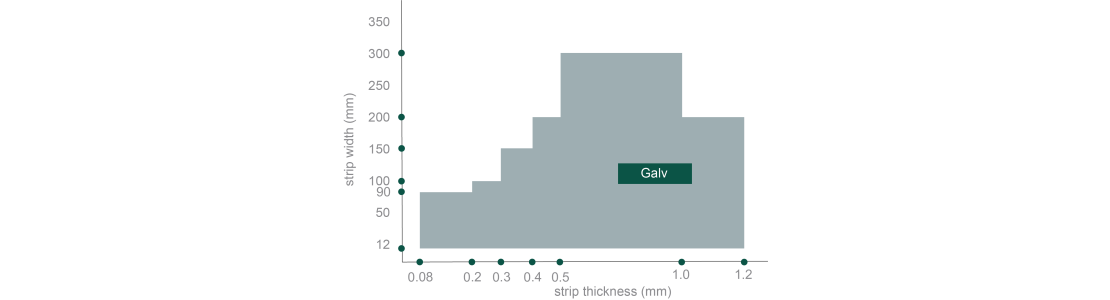
- *IMP: (copper-tin) Inter-Metallic Phase
- **Coating thickness ≤ 2 µm available upon request.
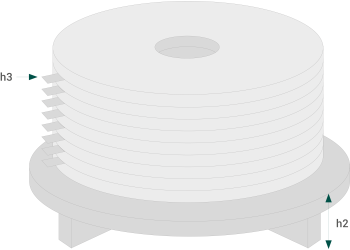
- Vertical axis ("eye to sky") pancake coils
- Pallet size: from 800×800 mm to 1500×1500 mm
- Coil dividers: wooden battens or card inserts
- Wooden crates also available
- Coil cradles min. 280 mm width at 5.7 kg/mm
- Horizontal axis ("eye to wall") pancake coils
- Coil cradles min. 280 mm width at 5.7 kg/mm
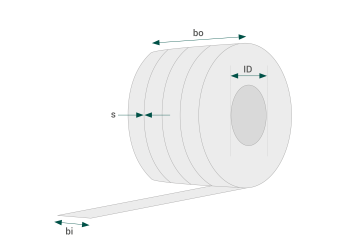
- Traverse wound coils
- Narrow strip is wound on a drum, traversing from side to side (like thread on a reel); coil ends are welded together, forming a much longer coil.
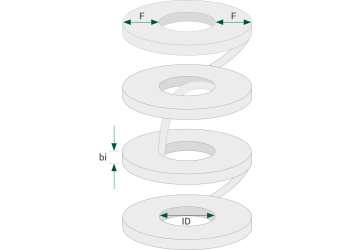
- TECSTRIP® Multilayer
The cost-effective coil of Copper, Bronze and High Performance STOL® alloys. Specially-joined individual pancake coils that offer uninterrupted full-quantity stamping. This gives you better productivity and lower costs when processing our alloys.
TECSTRIP® Multilayer comprises several coils (actual number depends on strip width) supplied on a pallet, which offer non-stop processing. The coil ends are welded together to effectively form one very long coiled strip. TECSTRIP® Multilayer decoils continuously in an inwards and outwards manner during processing, so the operator no longer needs to stop and re-start the machinery.
Your Contacts
KME Stolberg GmbH - Chicago IL
North America Sales Center